One issue that older hospitals face with surgical instrument inventory is that inventory gets managed on a “Just in Case” basis, rather than “Just in Time”. i.e. A hospital starts carrying more inventory than required, just in case the surgeon demands or just in case the right instruments are not available at the right time.
We studied the inventory patterns at the Cardiac Department of a Multi-Speciality hospital, a reputed 400+ bedded Hospital. This department conducts 5-8 cardiac surgeries per day.
Here is the inventory of sets:
Total no of unique set types (cardiac) | 46 |
Types of Chest Tube Thoracostomy sets (CTT) | 10 |
Types of Doctor-specific sets | 15 |
Others | 21 |
A closer inspection of the CTT and Doctor sets revealed some interesting facts:
- The 10 different CTT sets had a similarity measure of 82-100%, which means atleast 96 out of 118 total instruments were common to all sets. 4 of these 10 sets had a similarity of more than 90%.
- In the case of Doctor specific sets, 11 out of 15 sets had similarity of 90% and above. i.e. 42-45 instruments out of 46 were common to all sets.
- All these sets had shortfall of instruments (means not all instruments were present in the set).
- All these sets had mismatch of instruments (instruments in the set did not match the set checklist).
How does this impact the surgical instrument workflow?
- Surgeons and scrub nurses complain that set instruments are always mismatched.
- With a manual system, users packing the set have a harrowing time keeping track of 25 different set checklists rather 1 or 2 standardized ones. The existence of mismatch in sets points to this fact.
- User confusion at the cardiac department to know which set contains which instruments. This, once again, results in wasted cycles, when sterile sets have to be needlessly opened to find a particular instrument.
- Burden of keeping inventory of 1,180 different instruments for 10 different CTT sets. The financial implications of wear and tear and replacements can only be a guesstimate. (for doctor sets, these translate to 700 different instruments for 15 different sets.)
- Higher work burden in instrument separation, reconciliation, reprocessing, etc.
What could be done to correct this?
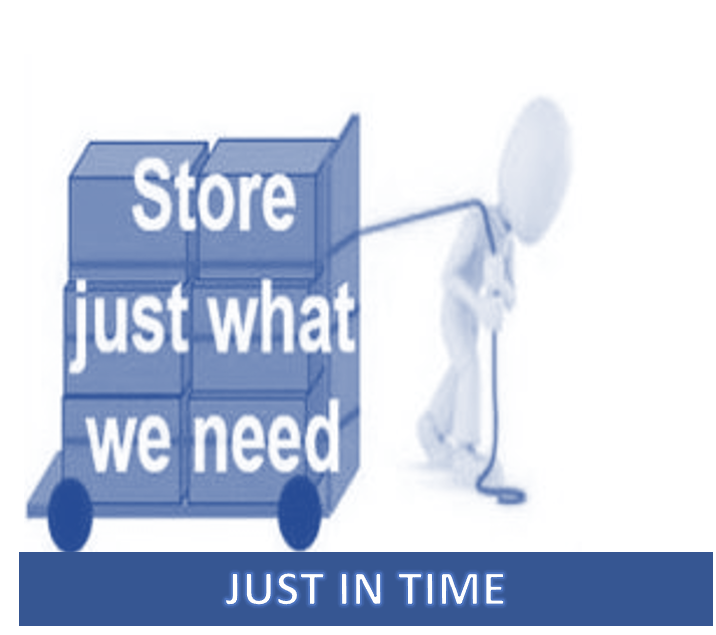
- Standardize sets around common instruments and have loose packs for unique instruments, so that doctor requirements of unique instruments are met. This will also simplify a user’s task since instead of keeping track of 10 or 15 different set checklists, the user must deal with only 2.
- Reduce total no of sets once standard sets are available, since you probably need fewer standard sets with doctor specific loose packs.
- Barcoded unique IDs on instruments can help users complete the packing process through instrument scans rather than manual matching.
Our team at Healthtech Pivot doesn’t just help you onboard inventory as is; it partners with you to simplify processes and review your entire surgical instrument inventory. Over time, the benefits are tremendous – helping you to right-size your inventory and simplify processes.
Trackbacks/Pingbacks